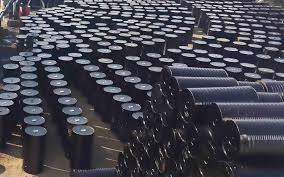
Blown Asphalt 85/35:
Blown Asphalt 85/35 or Oxidized Bitumen is produced by blowing hot air into the penetration bitumen. This action makes the bitumen more rubbery than its original formula and it becomes harder bitumen.
This bitumen recovery the weight loss under heating. Due to low thermal sensitivity, the softening point is much higher than regular bitumen and the penetration index (PI) is higher than road construction bitumen (8>PI>2) due to the letter has a gel-like structure because of asphalt accumulation.
Blown Asphalt 85/35 is produced by the air-blowing of penetration grade bitumen.
This is done at high temperatures, resulting in a material of a much higher penetration index.
Chemical Mine World Oxidized Bitumen 85/35 is based on petroleum bitumen which is made by blowing bitumen 60/70 by very hot air.
The designation of the Blown Asphalt 85/35 refers to the midpoint of the softening point acceptance criteria.
Chemical Mine World Oxidized Bitumen 85/35 is produced by either Continuous or Staggered Blowing Process.
Heated Penetration Grade Bitumen under controlled environment is blown with air which controls the Oil Content in the Bitumen while it oxidized.
The different grades for suited applications produced are designated by two numbers to indicate the mid-points of their softening point and penetration ranges.
Blown Asphalt 85-35 is based on petroleum bitumen which is made by blowing bitumen 60/70 by very hot air.
In addition, the numbers relate to the midpoint of the material’s softening point and penetration respectively.
The softening point value measured by Ring and Ball method as determined by ASTM D36. Also, the penetration value is in 1/10 mm as determined by IP49 or ASTM- D5.
Application of Blown Asphalt 85/35:
Oxidized asphalt 85/35 uses in the chemical, fuel, paints, lacquers, varnishes, paper-pulp-board, textile processing, road construction, pavement ,crack seal and repairmen, civil works, roofing, construction industries; sealing and insulating buildings, adhesive, construction materials additive, dust-binding, coating, insulating and impregnating agent, make rubber and plastic products.
The blown asphalt 85/35 products are for paving, roofing; also used in asphalt based paints for corrosion protection of metals, in lining public works structures, adhesives in electrical laminates, base for synthetic turf; typical uses for oxidized asphalt 85/35 include roofing, pipe coating, Portland cement pavement, hydraulic applications, paint manufacturing.
Technical Advantages of Blown Asphalt 85/35:
- Durability
- Flexibility
- Water Resistant
- Chemical Stability
Compared to paving grade bitumen:
- Reduced temperature susceptibility
- Exhibits a more ‘solid’ nature at ambient temperatures
- High penetration index
Handling / Storage:
Heating of packaged bitumen is a critical phase in most of the final uses. Typically, the packaged material is heated and melted in boilers out on site.
However, control at the heating phase is very important in terms of health and safety as well as in maintaining the quality of the product.
Note must be taken of the maximum safe handling temperature of 230 C and this should not be abused. Bitumen is a poor conductor of heat, consequently, control of the heating phase is of paramount importance.
The Blown Asphalt material should be broken up prior to placement in the boiler. This exposes a larger surface area to the heat and encourages a more even heating regime. Without the larger exposed surface area, aggressive heating at the base and sides of the boiler may well result in localized overheating, altering the characteristics of the Chemical Mine World modified bitumen and potentially causing thermal cracking of the bitumen, creating the release of low lash vapors.
The flash point of the blown asphalt then becomes irrelevant; as these low flash vapors determine the fire risk.
Melted bitumen should not be left in the boiler and reheated from cold, as there is then a high potential for localized overheating around the heating area (lack of convection means poor heat transfer) and potential development of a pressurized pocket of low flash vapors.
Be aware of the placement of any temperature monitoring or control devices. As a result of the poor thermal conductivity of the bitumen, a thermometer in the bitumen some distance from the heat source could read significantly different (even hundreds of degrees) from the true temperature of the bitumen near the heat source.
Health & Safety:
Workers should wear protective masks, gloves, and goggles during application. The asphalt can be removed from equipment and tools with kerosene or gasoline. Care should be taken when heating Blown Asphalt 85/35 to avoid overheating. For Health and Safety information, please make reference to the relevant MSDS.
Packing of blown asphalt 85/35:
The Chemical Mine World is manufacturer of blown asphalt 85/35 in various packing including kraft bag, meltable plastic bag, drum and bulk blown asphalt 85/35 from penetration grade bitumen, which is blown by hot air in a controlled process until the desired specification is reached.
The Chemical Mine World oxidised bitumen 85/35 can be supplied in any grade and are designated by two numbers to indicate the softening point and penetration ranges. The oxidized asphalt grade 85/35 means softening point is 85°c and penetration is 35 desimillimiter is produced in compliance and conformity to ASTM standard and meets the following specification.
Data Sheet of Blown Asphalt 85/35:
Bitumen 85/35 | Test method | Unit | Specification |
Specific gravity @25/25 C | ASTM D70 | (Kg/m3) | 1.05 approx. |
Penetration @ 25°c | ASTM D5 | mm/10 | 30/40 |
Softening point °c | ASTM D36 | °C | 80/90 |
Ductility @25 °c | ASTM D113 | Cm | 1.5 min |
Loss on heating(wt) % | ASTM D6 | Wt. % | 0.2 max |
Flash point °c | ASTM D92 | °C | 250 min |
Solubility is CS2(wt) % | ASTM D4 | Wt. % | 99.5 max |
Spot test | A.A.S.H.T.O 102 | — | Negative |